Hydraulic Filtration Systems
Hydraulic filtration systems are vulnerable to three major issues:
1.With high operating pressures combined with close tolerances between moving parts require the system to be ultra clean. Hydraulic systems are "closed loop". Contamination by foreign matter such as highly abrasive silica 1 micron and above can cause immense damage. 2.Water contamination may emulsify oil leading to thickening and rusting of components. water contamination should be below 100 ppm (0.01%) for general hydraulic systems. 3.Excessive temperature, A ten degree rise above normal operating temperature will halve the life of the oil. Analysis results will show a rise in oxidation and a depletion of additives, the major reason for temperature rises are normally from picticulate and water contamination.
90% of breakdowns on hydraulic systems are shown to becaused by contamination in the oil
Standards that exists today
- Hydraulic oil cleanliness standards, for particulate matter (dirt and dust particles), are measured by ISO 4406 contamination code table.
- The accepted norm for hydraulic oils is a code rating of 18/16/13 for particles of 4, 6 and 14 microns.
- This translates to numbers of particles per 100ml of the oil that are deemed to be acceptable in any hydraulic system are 250,000 (4 microns), 64,000 (6 microns) and 8,000 (14 microns).
- Standard OEM fitted hydraulic filters are usually rated at b(10) = 75. This means that they will remove 74 of every 75 particles above 10microns from the oil.
- This sounds good but these rating drops dramatically as the particles become smaller and at 4 microns could be as low as b(4) = 2, thus removing only half of the particles of this size.
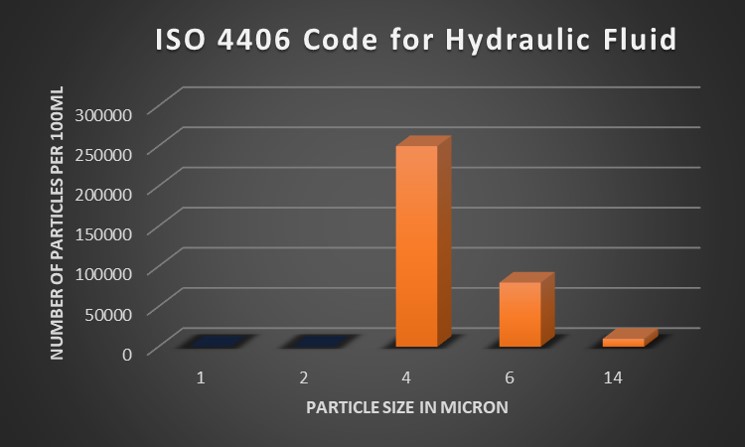
Particles for 18/16/13 ISO 4406 code rating
Particles below 4 Microns are UNFILTERED and increase exponentially WITH TIME
OEM Filters that are only rated to 10 micron, this means that all unfiltered contamination will continuously grow exponentially as indicated in the graph adjacent
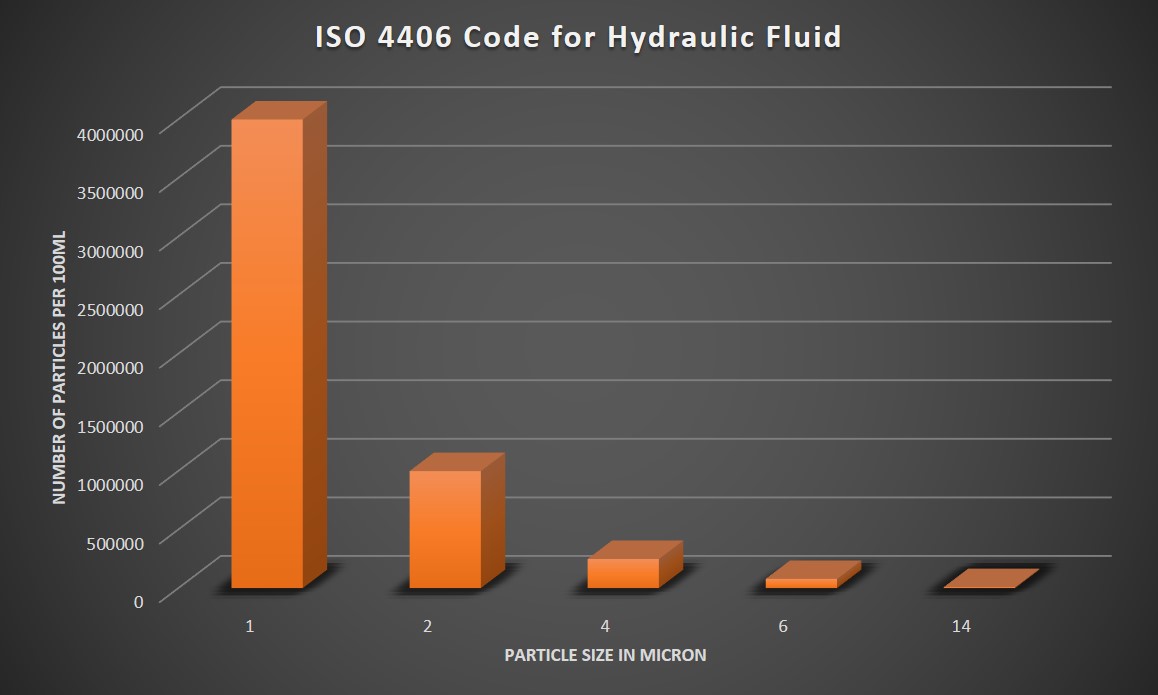
These huge numbers of particles cause major problems in hydraulic systems
- Dust and dirt trapped in the oil promotes foamingin the oil which reduces the oil's ability to lubricate the system.
- Microscopic air bubbles in the oil are compressed as they pass through the system and generate heat which thins the oil which reduces viscosity.
- increased slippage caused by the reduction in viscosity results in power wastage as more oil is bled back through the system clearance to the tank.
- If any moisture is trapped in the air bubbles it will be shed into the oil as it passes through the system.
- Moisture , Heat and Oxygen inbedded in the oil will become ACIDIC, which will cause dramatic componant failure
- Fluid contamination causes a grinding effect and this friction generates heat which requires additional energy to overcome, resulting in additional costs.
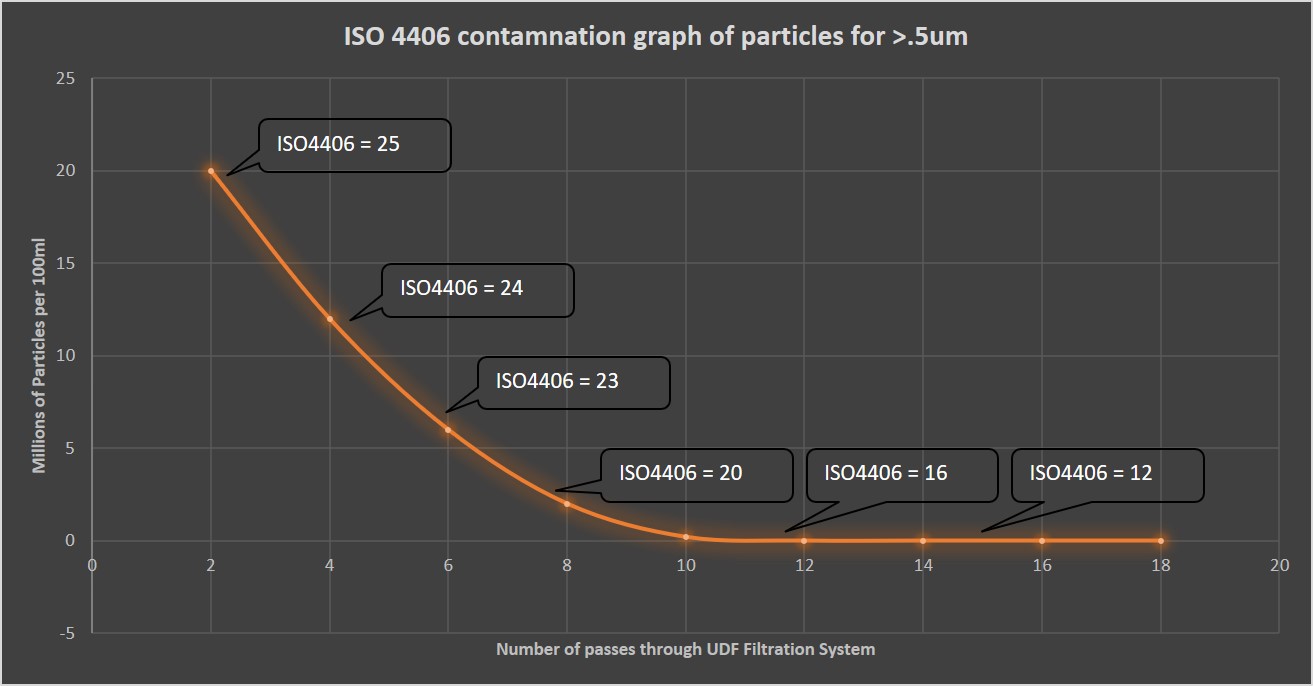
UDF hydraulic filtration systems remove 98% of particulate matter above 0.5 micron in size. Fitted on board as side loop, stand alone systems they progressively clean the oil continuously while the machine is in operation.
Continuous Filtration is better then periodic filtration or oil changes
The Graph below illustrates how a permanent UDF filtration system (red) is more effective than periodically filtering the system (blue) or the regular oil changes
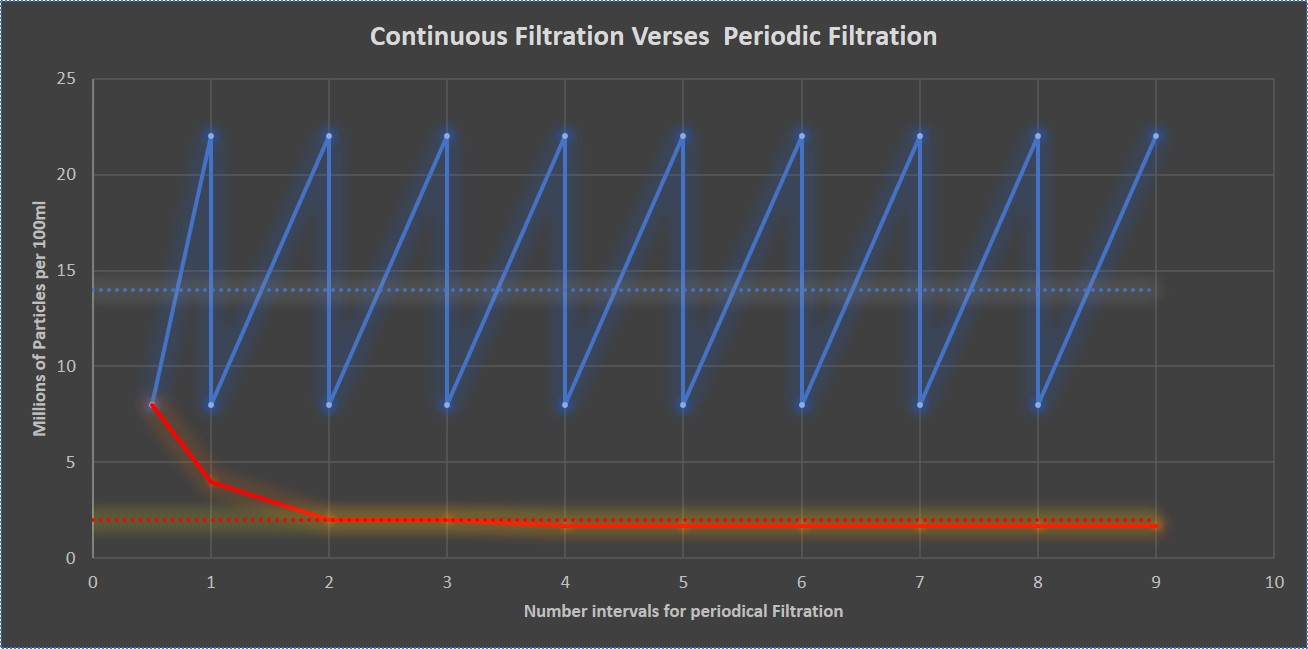
With a permanent UDF side loop filtration fitted the whole system in continuously cleaned extending oil and filter life, more efficient and cooler system operation and longer system component life. All of which means less costs and system failures.
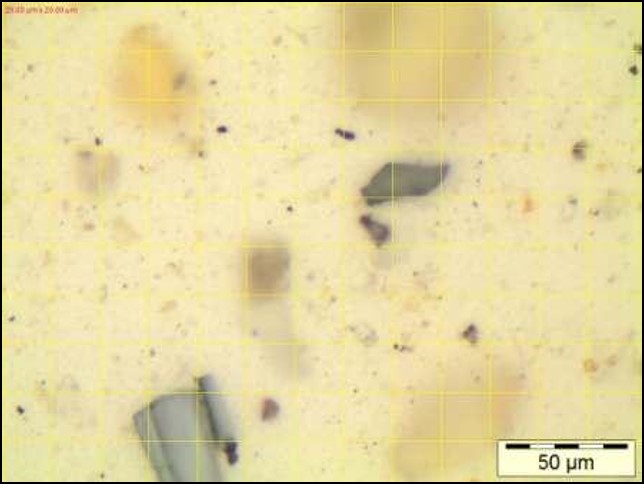
Visualisation of contamination in Hydraulic Fluid
These photomicrograghs magnified 500 times were taken from bulk storage fluid which was then filtered through the OEMs standard filter system and then through the UDF radial flow filter.
Left - Bulk Storage Hydraulic Fluid
Bottom Left - Standard OEM filtration -2 900 000 particles below 6 microns
Directly below - UDF Filtration - Unable to detect
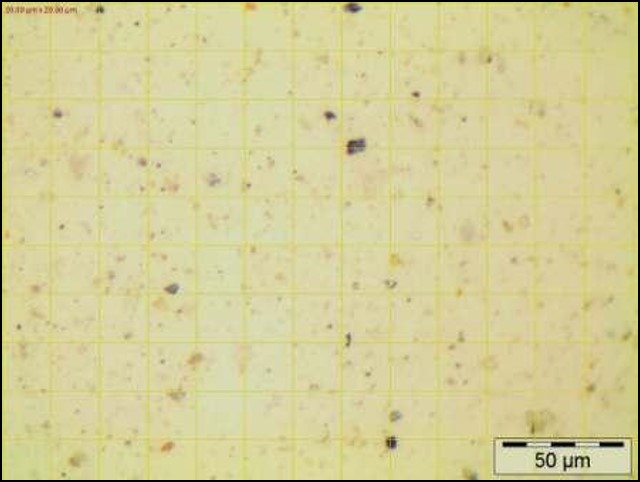
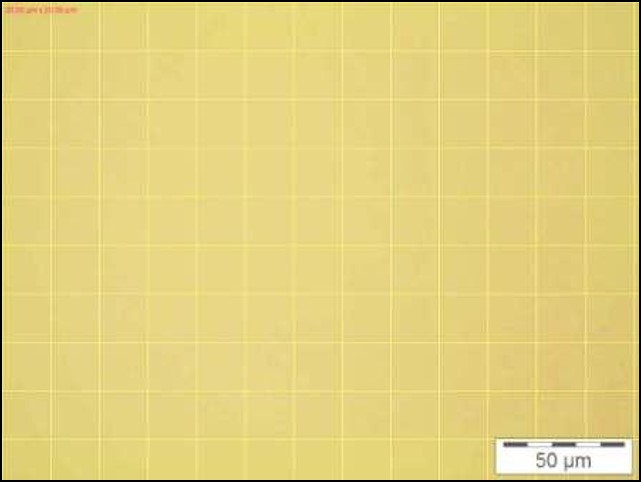
Schematic of Hydraulic Fluid Kidney loop Using UDF Filtration system
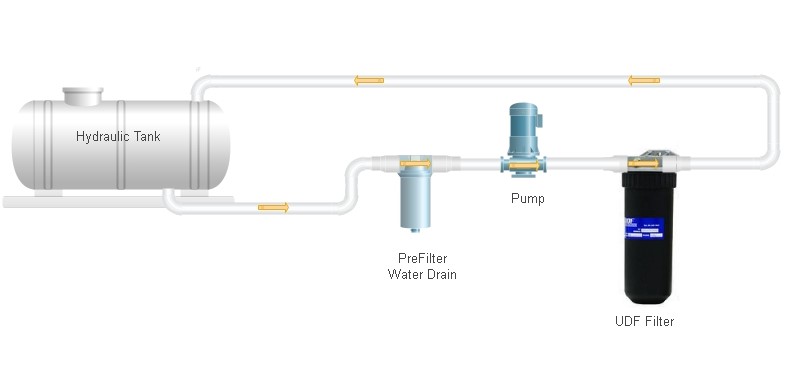
TP1
UDF filters are duel winding polyester and cellulose fibre sheets and act to sieve out and absorb contaminants in four different ways. They are not
designed as full flow filters and are fitted as additional filters in a by-pass configuration removing 3% of the total oil flow through a restriction orifice.
This oil is filtered and returned to the engine crankcase on a continuous basis.
UDF filters remove more than 98% of all particles > 0.5 microns that pass straight through the standard OEM filters and can thus be rated as
b(1) = 9 (minimum)
Applications :- Hydraulic Systems
HME / Transportation / Construction / Agriculture / Marine / Fixed Plant Industry
TP2
UDF filters are duel winding polyester and cellulose fibre sheets and act to sieve out and absorb contaminants in four different ways. They are not
designed as full flow filters and are fitted as additional filters in a by-pass configuration removing 3% of the total oil flow through a restriction orifice.
This oil is filtered and returned to the engine crankcase on a continuous basis.
UDF filters remove more than 98% of all particles > 0.5 microns that pass straight through the standard OEM filters and can thus be rated as
b(1) = 9 (minimum)
Applications :- Hydraulic Systems
HME / Transportation / Construction / Agriculture / Marine / Fixed Plant Industry
TP3
UDF filters are duel winding polyester and cellulose fibre sheets and act to sieve out and absorb contaminants in four different ways. They are not
designed as full flow filters and are fitted as additional filters in a by-pass configuration removing 3% of the total oil flow through a restriction orifice.
This oil is filtered and returned to the engine crankcase on a continuous basis.
UDF filters remove more than 98% of all particles > 0.5 microns that pass straight through the standard OEM filters and can thus be rated as
b(1) = 9 (minimum)
Applications :- Hydraulic Systems
HME / Transportation / Construction / Agriculture / Marine / Fixed Plant Industry