New Diesel Engine Standards
As Diesel injection technology has progressed, so has its sensitivity to contamination. With these new High Pressure Common Rail(HPCR) diesel engines having much improved power, fuel efficiency and lower exhaust emissions. To achieve these results, HPCR systems must operate with pressures of 2000 bar and above, injector openings ranging between 1-3 µm in diameter. For these HPCR systems the diesel fuel needs to be 20 times cleaner than ISO 4406 - 18/16/13 which is current standards vehicle manufactures adhere to with there installed filtration system.
Due to the new HPCR systems constraints, three common failures can be attributed to hard particulate contamination:
1. Mechanical failures occur due to component wear and blocking of movement.
2. Electrical failures occur when theres silting around the poppet valve stem, which causes injector solenoid burnout.
3. Performance failures occur as a result of blocked of injector nozzles and altering injector spray patterns.
THE EFFECT OF DIRTY FUEL ON THE operation of a diesel engine
The fuel is pressurised by the injector pump and delivered into a high pressure chamber, which is the so-called “Common Rail”. From this chamber, fuel is supplied to the different injectors and is constantly available. The fuel to be injected is controlled electronically by small valves in the injector which open and closes under electronic instruction. these components in the injector system operate with clearance between needle and the injector tip of 1 - 3 microns.
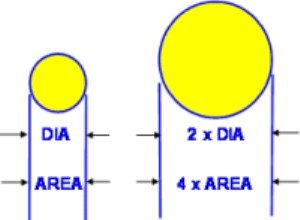
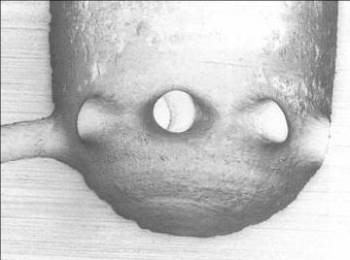
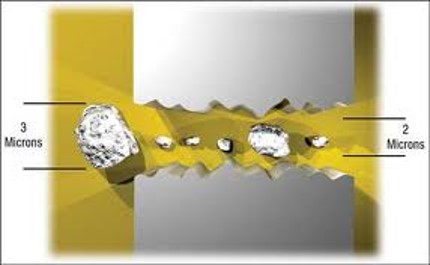
So what is the issue with dust contamination below 5 micron in fuel, well dust contains a high levels of Silica which is a extremely hard substance. On the Mohr Hardness scale, Silica is rated with a figure 7 where Diamond is rated with a figure of 10. Silica particles can easily cause wear damage on hard steel. These dust particles enter the space between the needle and the injector tip body, or between the plunger and the pump body, the particles cause wear and stickiness. The damage caused by these particles is wear and the result is excessive leakage along the needle and poor sealing on the injector tip seat. The stickiness and poor sealing of the needle, causes the poor spray patterns. The wear caused by the dust particles can also cause a lack of pressure build up from the supply pump due to internal leakage
The injector will close much slower and allow fuel into the cylinder for a longer period of time which results in over fuelling.the area of the needle and seat small particles of dirt are trapped between the two relatively moving parts and do not allow the injector to close properly. This will cause the injector to dribble non-atomized fuel onto the piston crown.When over fuelling and/or dribbling occurs this fuel does not burn correctly and is carried down into the lubricating oil past the piston rings where in a chemical reaction it forms sludge. This destroys the properties of the oil and its ability to protect the internal moving parts of the engine
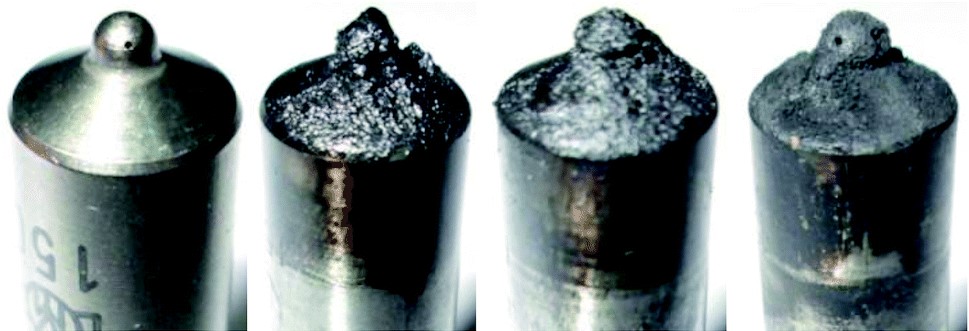
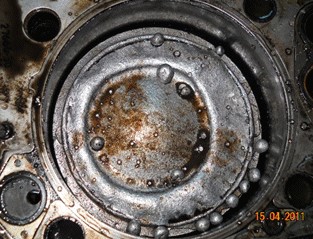
Cylinder glazing and excessive oil blow by also occur when the fuel is not properly atomized and impinges on the walls of the cylinder. This un-burnt fuel bakes onto the cylinder wall in a hard layer which the piston rings cannot remove
Nozzle coking caused by dribbling injectors
Fuel additive technology has solved this type of internal deposit build-up but there is another aspect to nozzle coking that needs to be addressed.
The fuel from dribbling injectors collects in this cup where it is baked by the heat in the combustion chamber and forms hard gummy deposits which block the spray holes from the inside and is also visible externally

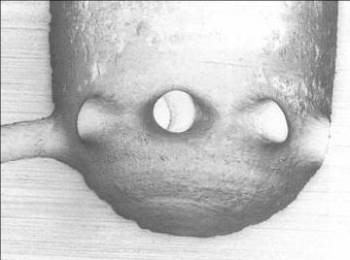
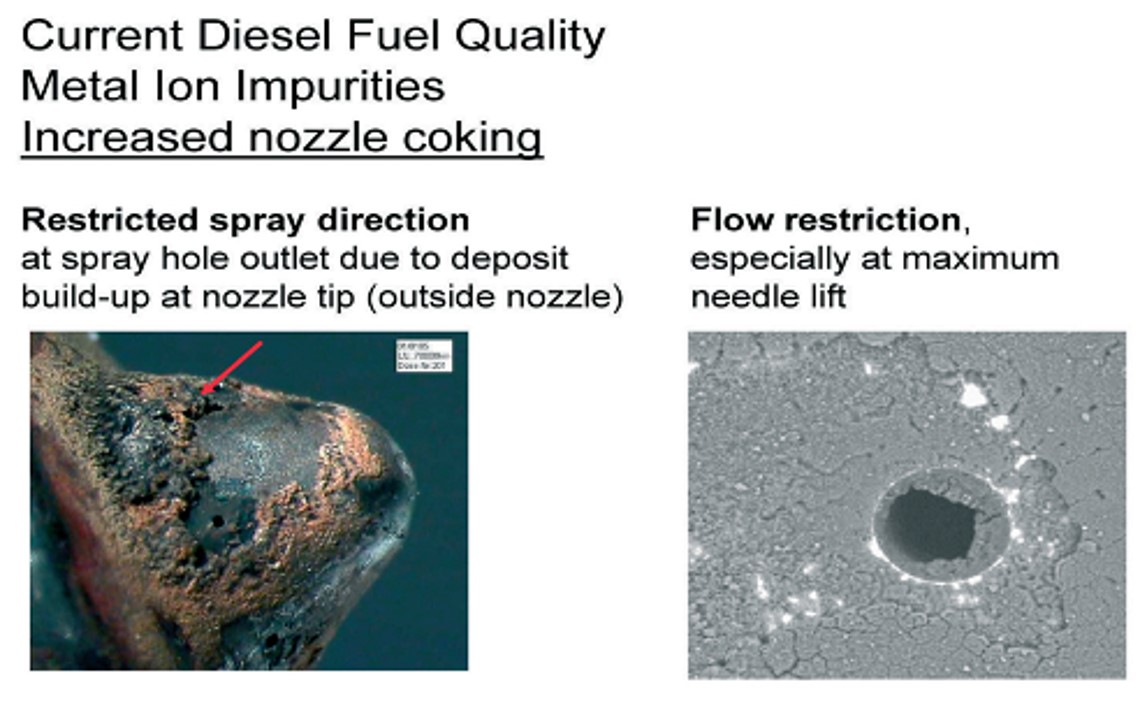
Fuel and lubricant derived ash can contribute to coking on injector nozzles and will have a significant effect on the life of diesel particulate filters. Ash-forming metals can be present in fuel additives, lubricant additives or as a by-product of the refining process.
What effect does dirt have exhaust gas emissions?
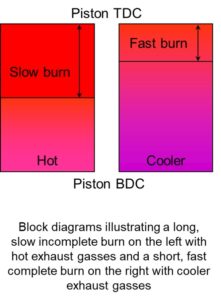
As discussed in the previous point dirt affects the smooth operation of the needle in the barrel and can cause the timing of the injection of the fuel into the cylinder to be incorrect. This small amount of time is enough to cause a delay in the combustion of the fuel in the cylinder and therefore the amount of torque and power produced is much reduced. A delay in the closing of the injector will result in over-fuelling and a long burn time and un-burnt fuel being thrown out into the exhaust system. This fuel undergoes a chemical change within the hot exhaust gases producing hazardous and harmful by-products.
Lubricity
When two or more solid items move relative to and in contact with each other they are subjected to friction between the touching surfaces and this friction produces heat and wear. Lubricating fluids are used to separate these parts thus reducing the effects of friction by replacing solid fiction with fluid friction.
In a diesel fuel system the components that need lubricating are the fuel pumps and the fluid used to carry out this lubricating function is the diesel fuel itself. To be able to do a proper lubricating job this fuel needs to be free of dirt as this will interfere with the dynamic clearances between the moving parts. The hard dirt particles gouge and tear out pieces of the surface material and this now increases the quantity of contamination in the fuel.
Dirty fuel has the same effect as grinding paste and will not only shorten the life of components but also increases pump slippage as tight tolerances are destroyed and the operational efficiency of the component decreases. In some cases the dirt and wear particles produced can cause partial or complete seizure of the pump components
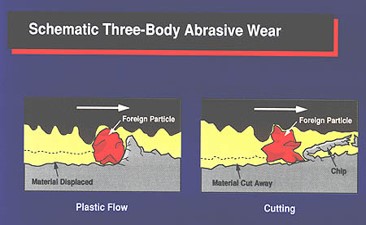
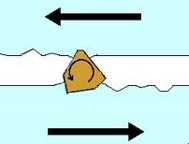
These factors lead to excessive fuel consumption, elevated exhaust gas temperatures and turbo failures, inefficient operation, short injector life, much reduced engine life or catastrophic engine failure
How can these problems be rectified?
Ultrafine Depth Filtration (Pty) Ltd manufactures a range of ultra efficient depth filters that will remove 98% of 0.5 microns and greater particles that standard filters fitted as OEM parts cannot. These filter systems are also unaffected by vibration and pulsating flow. The performance of UDF filter systems returns great value to the end user that has the foresight and knowledge to fit them.
UDF filters provide 20 times better filtration than the standard filters provided by the OEMS in your equipment. The UDF filter continuously removes contamination (dirt, combustion, oxidation and abrasive particles) down to 0.5 micron and thus improving the lifecycle.
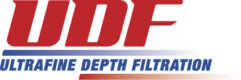
MP101
UDF filters remove more than 98% of all particles > 0.5 microns that pass straight through the standard OEM filters.
Applications :-Diesel Vehicle
4×4’s / Recreation Vehicles (RV’s) Sport Utility Vehicles (SUVs)
Double Cab / 1Tonners
TD4
UDF filters remove more than 98% of all particles > 0.5 microns that pass straight through the standard OEM filters.
Applications :-Diesel Vehicle
4×4’s / Recreation Vehicles (RV’s) Sport Utility Vehicles (SUVs)
Double Cab / 1Tonners
TP1
UDF filters remove more than 98% of all particles > 0.5 microns that pass straight through the standard OEM filters.
Applications :- Industrial Diesel Vehicle
HME / Transportation / Construction / Agriculture / Marine
WT1
UDF Pre-filter/water separator will remove remove up to 95%of all particles larger than 6 microns in size and all water contaminating the fuel. This water must be drained off before the level reaches a distance of 20 mm to the bottom of the cartridge.
The filter bowl has a red float indicator to easily show water contamination
TP2
UDF filters remove more than 98% of all particles > 0.5 microns that pass straight through the standard OEM filters.
Applications :- Industrial Diesel Vehicle
HME / Transportation / Construction / Agriculture / Marine
wt2
UDF Pre-filter/water separator will remove remove up to 95%of all particles larger than 6 microns in size and all water contaminating the fuel. This water must be drained off before the level reaches a distance of 20 mm to the bottom of the cartridge.
The filter bowl has a red float indicator to easily show water contamination
TP3
UDF filters remove more than 98% of all particles > 0.5 microns that pass straight through the standard OEM filters.
Applications :- Industrial Diesel Vehicle
HME / Transportation / Construction / Agriculture / Marine
WT3
UDF Pre-filter/water separator will remove remove up to 95%of all particles larger than 6 microns in size and all water contaminating the fuel. This water must be drained off before the level reaches a distance of 20 mm to the bottom of the cartridge.
The filter bowl has a red float indicator to easily show water contamination